Cement works
& Mines
For more than 25 years, Lubrilog is specialized in production of very high quality lubricants for the lubrication of Open Gear Drives in raw material industries (Mining industry, Cement plants, Fertilizer industry, Power stations (coal), Steel, Aluminum, Chemical, Environment, etc.)
In this way, Lubrilog proposes lubricants for Open Gear Drives but also for fans bearings, Lepol® grate bearings, inlet seals of rotary kiln, floating kiln tyres, etc. Our skills have allowed us to obtain the FL SMIDTH approval for the whole of our range, in addition to our current approvals METSO MINERALS, FIVES FCB, ALSTOM, FERRY CAPITAIN, CMD, etc.
Our technical department is able to provide an analysis or an advice for each plant anywhere in the world thanks to its experts in Open Gear Drives lubrication. Lubrilog offers free technical support to all its customers through regular visits to plants and detailed reports of the monitoring equipment.
We have also developed an innovative cleaning solution in service : Lubriclean EP.
Considering the cost of a production shutdown of a kiln or a mill, this solution enables in 1h30 maximum and without production stop, to ensure a cleaning of the equipment and to extend its life time (by reducing abrasive wear).
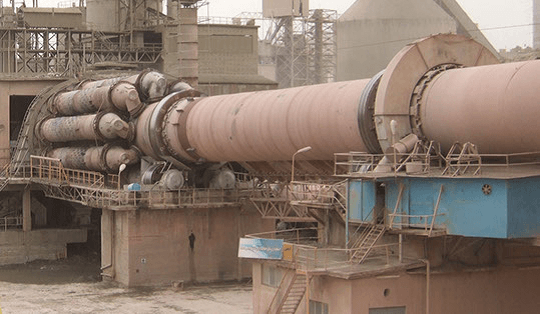
Our references
Cement plants customers : LAFARGE HOLCIM, HEIDELBERG, VICAT, SECIL, etc.
Mining industry customers : CODELCO, ANGLO-AMERICAN, MANAGEM, etc.
Applications
Open Gear Drives : Priming
Based on its experience, Lubrilog has developed a running-in process for large open gear drives, providing a maximum security and a long life.
After erection and setting-up of the drive (girth gear and pinions), Lubrilog recommends proceeding in two steps for which specific products were developed.
Priming is the initial lubrication of the gear set. Immediately after the end of the mechanical settings a thick coat of specific and very sticky lubricant containing graphite is applied manually on the working flanks (with brush, without air inclusion, on the previously cleaned surfaces). All other teeth surfaces have to be covered as well, but in lower quantity.
Main functions of the initial impregnation are:
- Avoiding corrosion.
- Obtaining a perfect protection by forming an efficient lubricant film from the first teeth contacts (despite the initial surface states and the medium contact quality).
- Assessing the running time loading in order to be able to correct mechanical settings if necessary.
Open Gear Drives : Running-in
The running-in phase is very important and determines the shelf life of the open gear drive.
Indeed, damages can appear very quickly after the start-up stage. Even with very good mechanical settings, surface states are not perfect and the initial contact may represent only 50 to 60% due to machining or geometry imperfections.
In order to respect the mechanical constrains for which the girth gear was calculated, it is very important to use a running-in lubricant (slow lapping without abrasive particles) to improve the state of working flanks. This is achieved by distributing over a larger surface the transmission and the effective power.
The running-in procedure is different depending on the machine driven by the gear set (mills in cement plants or coal power stations, kilns, etc). Therefore, it is necessary to respect the manufacturer’s instructions concerning the loading steps.
Open Gear Drives : Spraying
The following table shows the range of greases and oils suitable for spray lubrication (spraying of lubricant on the working flanks). Lubrilog helps you to find the best lubrication parameters (choice of the lubricant, amount to apply and lubrication intervals, preventive maintenance controls to be carried out).
Open Gear Drives : Cleaning & Repair
For situations that might be challenging for the good performance of the open gear drives, Lubrilog has developed repair and cleaning solutions.
Repair or cleaning operations can be performed while operating, without production loss.
The repair lubricant, Grafolog RPR (which has to be applied by a Lubrilog specialist) is intended to eliminate some defects (scuffing, marks of foreign bodies, etc.) and to obtain a satisfying loading surface within a very short time.
This operation does not exempt from geometrical setting of the drive and should it be necessary it can be completed by a mechanical intervention at standstill (grinding).
The cleaning solvent, Lubriclean EP has been developed for cleaning (in maximum 1 hour) large open gears exposed to very high abrasion (nature of the treated material, poor state of housing’s sealing). Lubriclean EP can be applied as a preventive operation or before a maintenance shutdown.
Tech Team Service
Lubrilog has a technical department (Tech. Team Service) exclusively dedicated to these industries. Wherever your plant is located, a Lubrilog technician will always be available on site to realize a technical visit or assisting you for the implementation of our solutions (lubricants, equipments, services).
Lepol® grate bearings lubricants
Traveling grates Lepol® (designed by the Company POLYSIUS) are used for cement manufacturing process called “semi-dry process”.
Lepol® preheater grates is an exchanger where the smokes, coming from the rotary kiln operating at about 1000°C, cross the bed of pellets. During this exchange, the pellets are dried and partially decarbonised (20 to 30%). They enter into the kiln at 840°C. Traveling grate bearings next to the kiln (internal or external) are submitted to very high temperatures. Results obtained with our grease Starplex G 1 are remarkable (in terms of lubrication quality and also consumption).
The application of our grease requires a centralized lubrication system.
Inlet seals of rotary kiln
Depending on the geometry of their sealing system, some rotary kilns are equipped with flat inlet seals that need to be lubricated with a grease (good temperature resistance is imperative).
For this application, Lubrilog has developed a specific grease called Starplex G 2.
The application of our grease requires a centralized lubrication system. It does not cause lubrication interruption by clogging (examples of application for the production of white and traditional cement).
Internal face of floating kiln tyres lubricants
The lubrication of internal face of floating kiln tyres is very important to obtain good service conditions (allow a movement of tyres on the kiln’s shell which is necessary due to difference of temperature between the shell and the tyre in order to avoid binding).
For this application, Lubrilog has developed lubricants with high graphite content.
Both lubricants that we propose have been used since many years by the most famous Groups using rotary drums:
Grakote Fluid High temperature paste with graphite
Grafolog 1278 S Compound “water + graphite” non-flammable
Grafolog 1278 S, compound “water + graphite”:
This lubricant is the best solution to comply with modern security standards applied in production sites. Indeed, Grafolog 1278 S never causes fire or pollution. Besides, this compound presents a significant cost advantage compared to the traditional pastes and greases.
Grakote Fluid, paste with graphite:
This high temperature liquid paste is based on synthetic oil and incorporates solid lubricants and contains additives which prevent from ignition.
Usually, both products are applied with manual spray system, once a week or every two weeks, according to the rotation conditions of the kiln.